Why You Need To Use Bore Track Data
We all plan the drilling and location of our boreholes in the best way we can use the tools we have. But what happens when those plans go unfavorably?
Bore track data captures the real journey of each drill hole. It reveals the deviations and azimuths that could make or break your project. A single wrong hole could potentially lead to devastating problems.
I call it the theory of the "Million Dollar Hole".
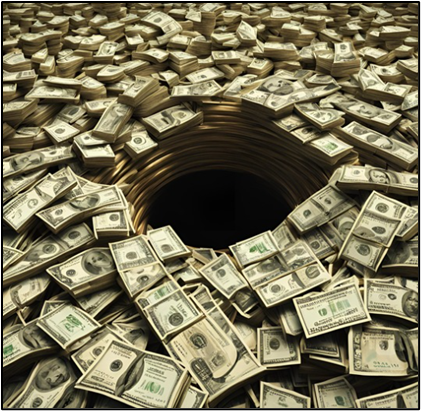
The Million Dollar Hole Theory
It's better to invest a bit more time and cost to redrill a wayward hole than to risk firing a rock into an undesirable location, potentially turning a simple hole into a million-dollar problem.
How do we avoid this completely preventable disaster? Bore tracking.
So what is bore tracking? Using a probe you drop down a borehole that measures and logs the actual path of the hole. Bore track logs are similar to drill logs, but they show the exact path each drill takes through the rock (including at specific intervals the inclination, azimuth, and length).
Often times the drilled hole matches the drill plan, but occasionally the bore track discovers deviations in the path of the hole. These deviations happen when the drill strays from its intended path, influenced by rock density, discontinuities, equipment issues, or human error.

The Ripple Effect of Deviations
Common problems from unmanaged hole deviations include:
1) Uneven Fragmentation
2) Overbreak and Underbreak
3) Safety Hazards (Fly Rocks)
4) Suboptimal Blast Performance
5) Increased Operational Costs
6) Oversize & Undersize
These problems happen when the toe from the hole has a big deviation in different azimuths, leading to areas where the energy of the explosive is going to be higher and areas where the explosive won't be effective. Below are specific factors that could take place:
Impact on Drill Load:
Deviations can skew the distribution of explosive charges, leading to uneven blasts and suboptimal results creating fines and boulders.
Formation of Oversized Blocks:
When drills don't penetrate deeply enough or they deviate from their intended path, the blast can leave behind oversized blocks or boulders. These boulders complicate the cleanup process, often requiring secondary breakage or causing significant issues for the primary crusher. If not identified early enough, they can become lodged in the crusher, halting the entire operation.
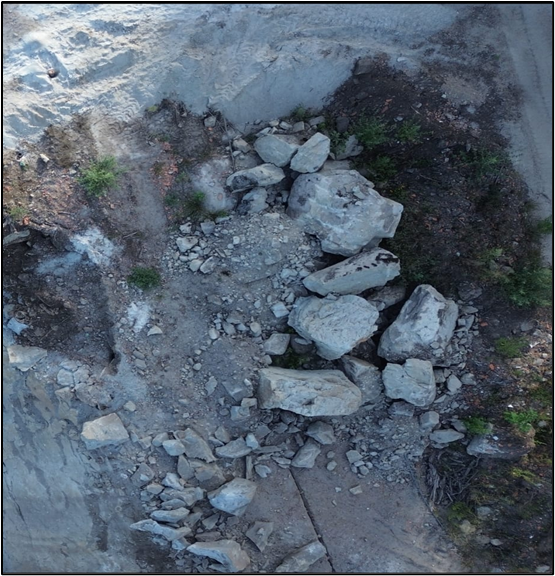
Fly Rock Hazard:
Significant deviations can lead to misdirected explosions, sending dangerous flying rocks into the air. Flyrock is a significant issue in blasting operations, posing serious safety risks and operational challenges. Fly rocks pose serious safety hazards, as they can travel unpredictable distances and directions.
These high-velocity projectiles can cause damage to property, and equipment, and, most importantly, endanger the lives of workers and nearby communities. Not to mention subjecting operations to potential claims and even lawsuits.
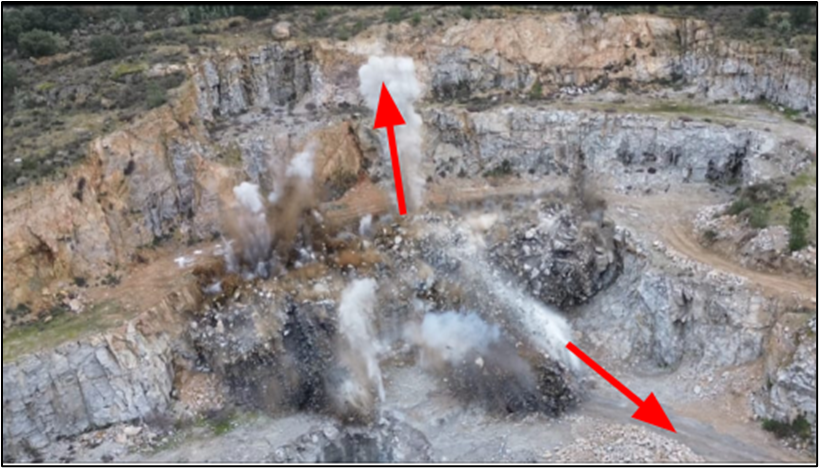
Drilling Deeper into Bore Track Data Analysis
Data Collection:
Advanced sensors and measurement tools track the drill's journey in real-time, capturing every inclination and azimuth usually meter by meter, or some even in real-time.
If the drill doesn’t collect this information, a borehole probe can capture the data after the borehole has been drilled.
3D Modeling:
First, drone photos can be used to create a 3D model of your bench. After the holes have been drilled, more bench pictures and AI can be used to locate your drill holes and pinpoint the collar.
After you have the position of your collar you can import the data from the bore track and start analyzing.
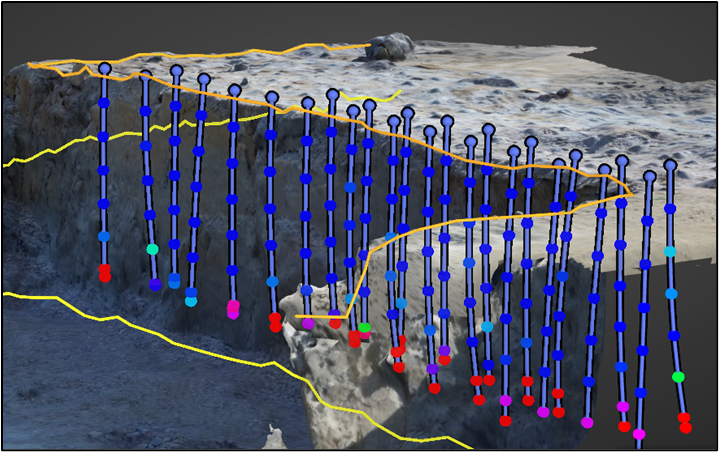
Interpreting the Data:
Use specialized software to analyze bore track data, identify problem areas, and plan corrective actions like modifying blast timing and loading plans.
Using Bore Track Data for Smarter Blasts
The benefits of Incorporating bore track data into your blast design are many including:
1) Reducing fly rock
2) Improving floor control
3) Bench maintenance
4) Drilling QA/ QC
5) Better fragmentation
6) Improved loading, hauling, milling
Reducing Fly Rock Risk
When the toe (the bottom end) of a drill hole deviates near the free face (the exposed surface of the rock), it disrupts the blast. The misalignment causes the explosive energy to be misdirected. Instead of breaking the rock uniformly, it creates uncontrolled forces that can eject rock fragments violently, leading to flying rocks.
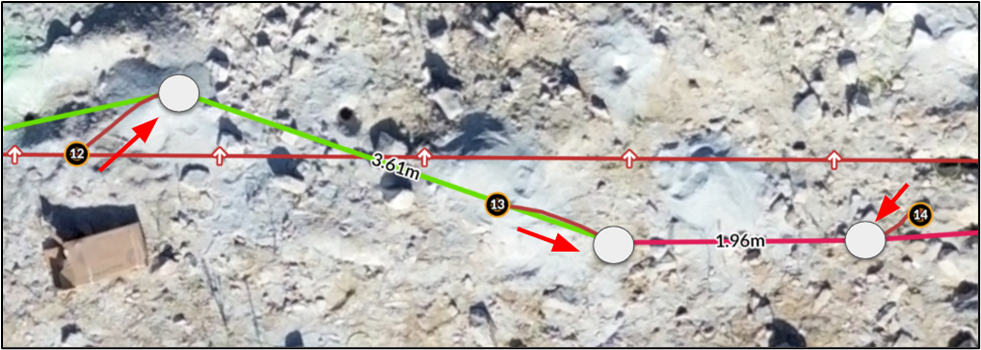
Through the software, we can calculate the burden for each hole and predict which holes could lead to fly rock.
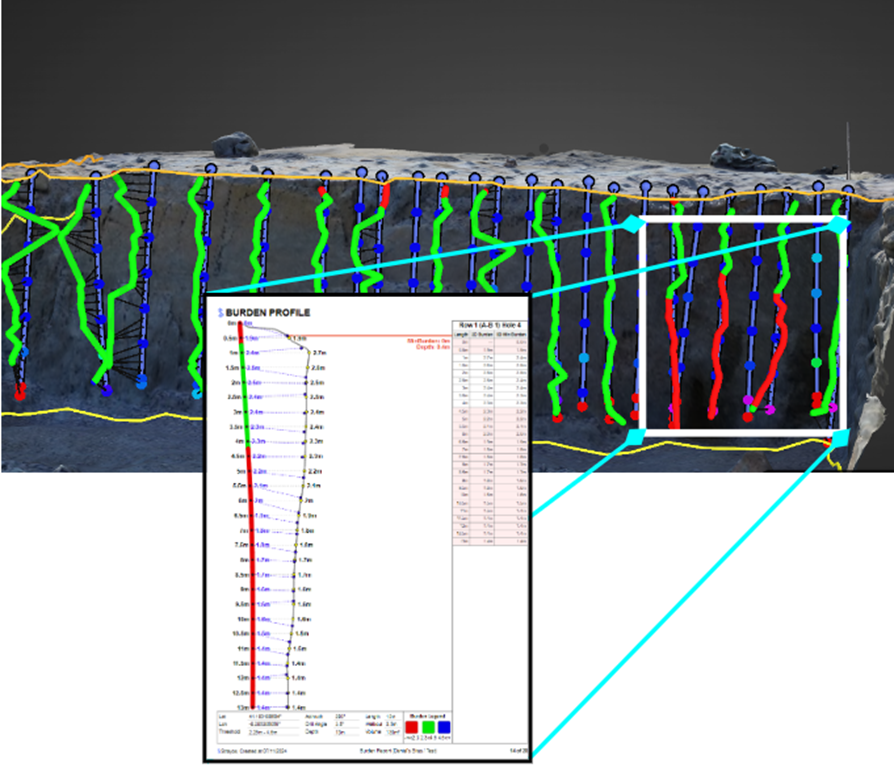
These values are detailed in a report, allowing you to analyze the burden distance from the hole to the free face throughout the entire hole.
Based on this data, we can determine whether the hole is suitable for the blast, whether we need to use decking during loading, or if redrilling the hole is necessary.
Floor Prediction
Another valuable analysis we can perform using bore track data and a 3D model is the prediction of the post-blast floor. By using the actual data on the length of the holes, we can generate a 3D and 2D prediction of the post-blast floor. This allows us to anticipate whether the floor will be uneven or irregular. An uneven floor can significantly complicate subsequent operations, making them more challenging and potentially increasing operational costs.
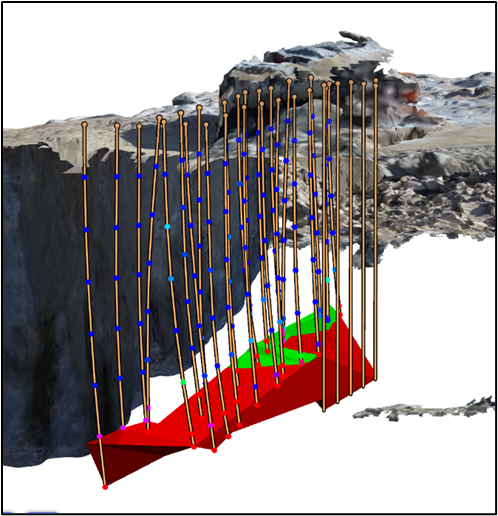
Fine-Tuning Drilling Operations:
Implement techniques like pilot drilling and guided systems to reduce deviations and stay on target.
Correcting Deviations:
Real-time adjustments and the use of specialized drill bits can help steer back on course.
Boosting Blasting Efficiency:
Use bore track data to ensure a more uniform distribution of explosive charges, leading to a cleaner, safer, and more effective blast.
Incorporating bore track data into your blast design is a smart way to put in a little more effort upfront to save big later. Whether its improving operational efficiency through better floors, loading, hauling, and milling. Or if it's better fragmentation with less ore loss and reducing the need for secondary breakage, or if you are looking to safeguard, your team, your equipment, or your legal bills from fly rocks, avoid the million-dollar hole and use bore track data to blast smarter.
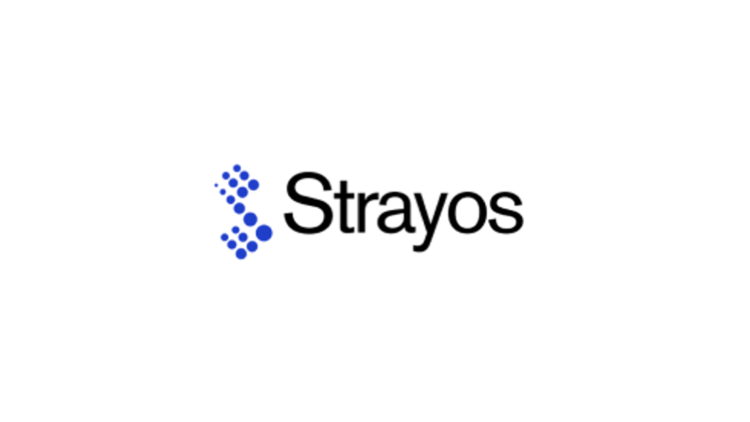
Check out our 2 Free E-books on AI applications for the drilling, blasting, and mining industries to see all the amazing advances that are available.
AI Guide for Drilling and Blasting
Watch our videos:
Follow Us on Social Media: