Three Tools for 2025 to Enhance D&B Performance
With the end of 2024, another year has passed where millions of pounds of explosives are consumed by operations to produce the raw materials we rely on.
Over the course of the year, Strayos has been lucky enough to work alongside several operations that aim to improve and optimize their operations, typically starting at the Drilling and Blasting process.
From countless hours of development, training, and implementation, Strayos provides valuable technology solutions to operations of all shapes and sizes. Many of the solutions are relied on day to day to maintain safe and efficient working conditions.
As we look back on 2024, we wanted to highlight the three most valuable tools that all D&B operations could use to help improve their work rolling into 2025.
1. Drill Designs and Design Surfaces
Strayos has developed a solution that can bring tremendous efficiency to the drill and blast design process when designing shots to a design surface. In many cases, quarries and mines have design surfaces (mine pans, new ramps, development shots, finish walls), where they are aiming to maintain grade in the field. Historic workflows would require GPS data to be staked out and then brought into modeling software to verify hole positions according to design parameters.
Strayos simplifies this process by allowing users to import their design surfaces to then precisely design their drill plans. Whether it is a 2D or 3D surface, above or below ground, it can be modeled. In many cases, uploading design crest and toe positions provides guidance for maintaining highwall design. For maintaining proper elevations, importing design surfaces for floor elevations or ramp designs can save a significant amount of time.
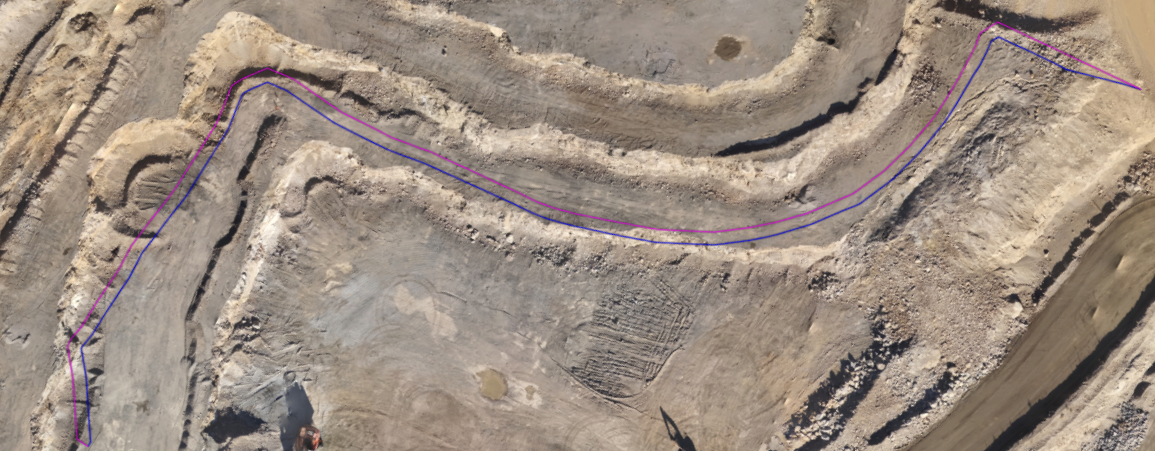
By overlaying design crest and toe positions, engineers can design their production blasts to comply with the mine design.
By uploading design crest and toe positions from mine plan, engineers can design shots to maintain highwall compliance
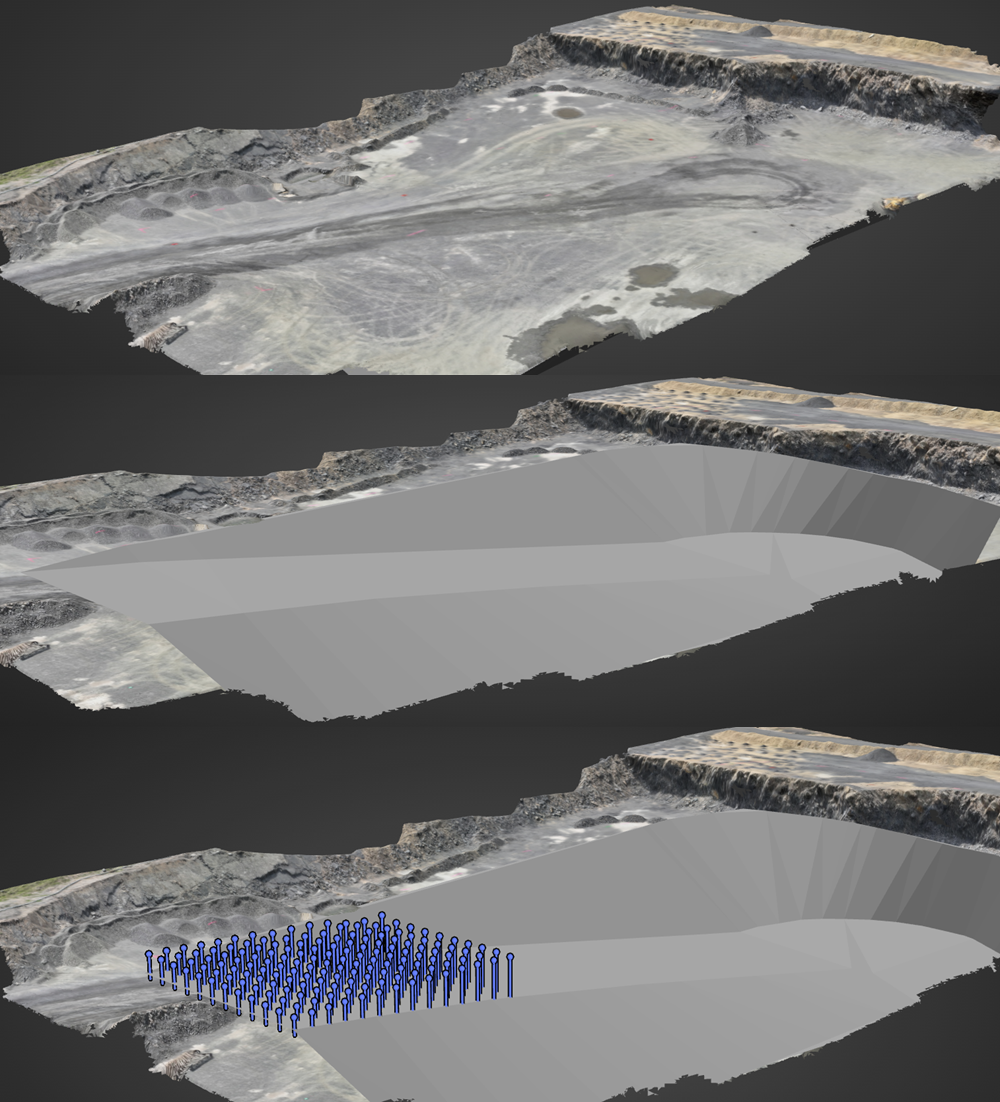
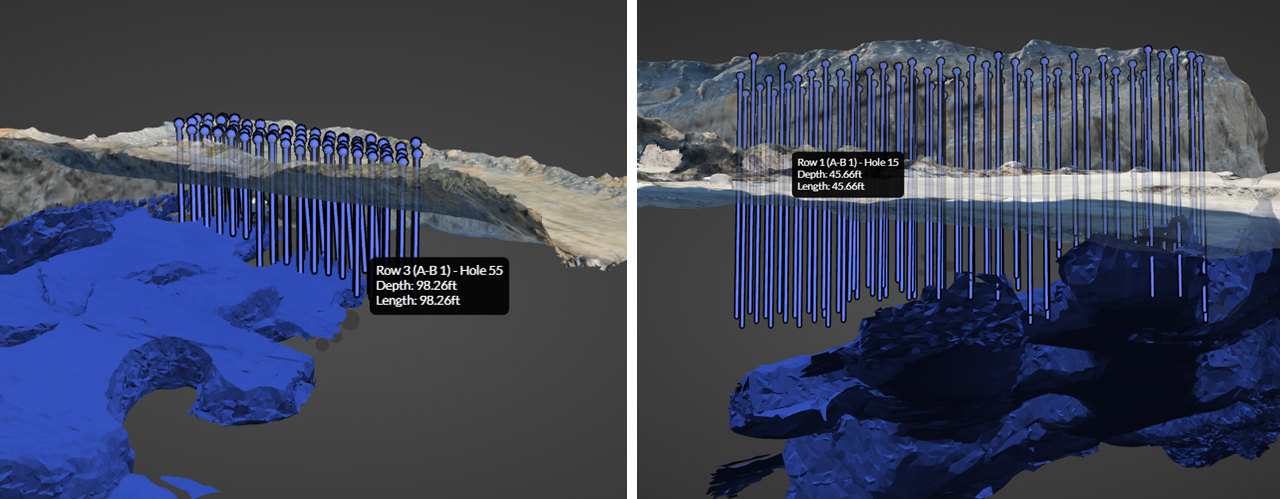
Finally, to evaluate the performance of a blast to the finish floor, Strayos provides an intuitive solution for comparing surfaces and previous shot designs.
2. Floor Control
When it comes to evaluating floors post-blast, it is important to understand where issues stem from. In many cases, excess drilling can create uneven floors as blasts are not being designed for specific elevations. In cases of excess drilling, backfilling may be needed to ensure loading operations do not dig below the finish grade. In other cases, loading operations may dig out sub drill leading to uneven floor elevations.
Surveying floors post blast can provide valuable data on elevation control. By overlaying shot designs, we can correlate grade issues to specific blasts or individual holes. Having the capability to compare as built conditions to design can also assist operations in understanding shot and digging performance.
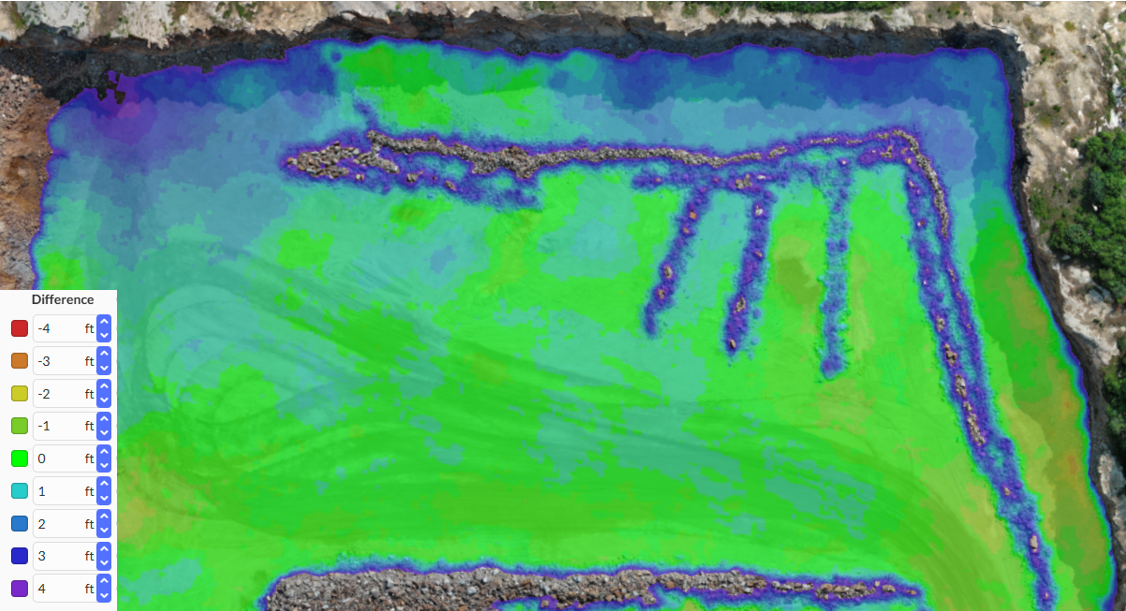
Strayos’ floor prediction tool creates a projected surface based on design or drilled hole depths. Having a visual of a floor surface from actual drill depths can help mitigate grade control issues as high and low spots can be proactively addressed by communicating the information to the loading operation.
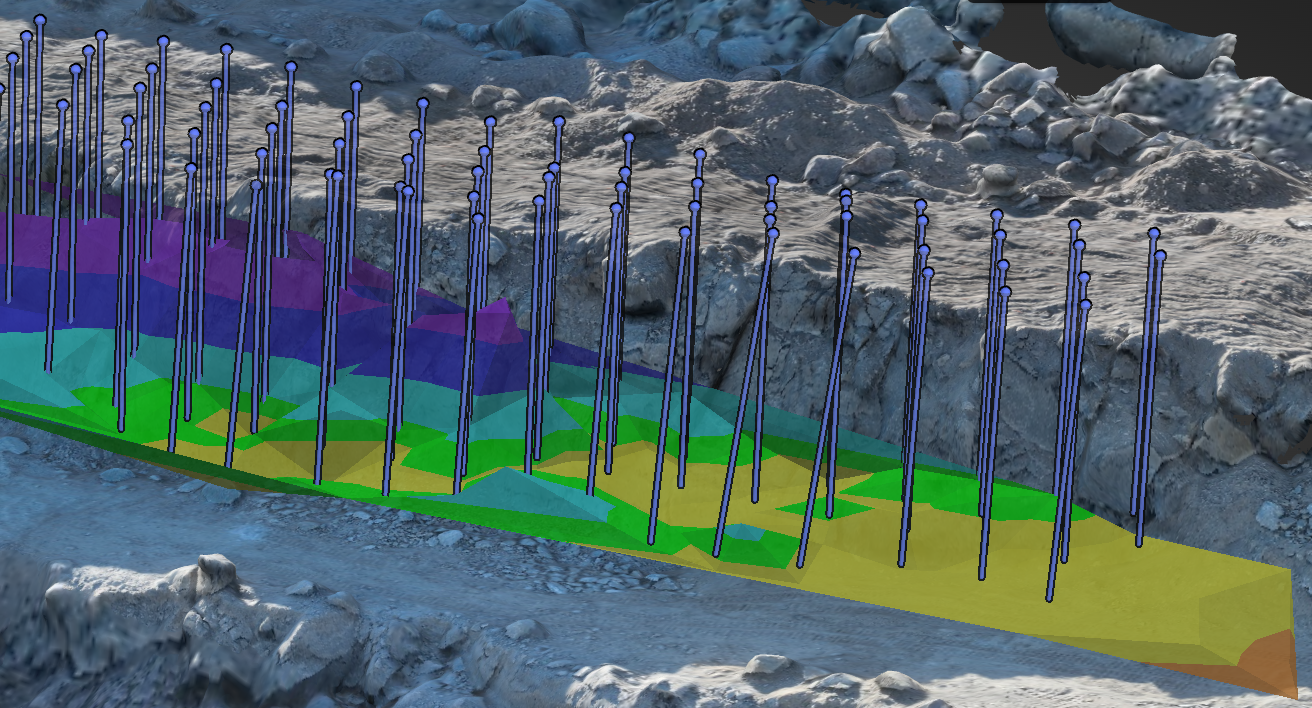
3. Post Blast Analysis
For continuous improvement of blast performance, Strayos makes it easy to compare pre and post-blast data. From fragmentation, blast movement, and back break analysis, engineers can dive into the performance of the blast in detail. By overlaying datasets, and viewing blast movement, engineers can analyze how their loading and timing affects their blast movement.
Fragmentation Analysis
Fragmentation Analysis allows you to easily see and quantify the effectiveness of your blast. See fragmentation size, and degree of passing, in 2D and 3D. Then match the fragmentation back to the blast design, drilled hole data, loading, timing, and even geology.
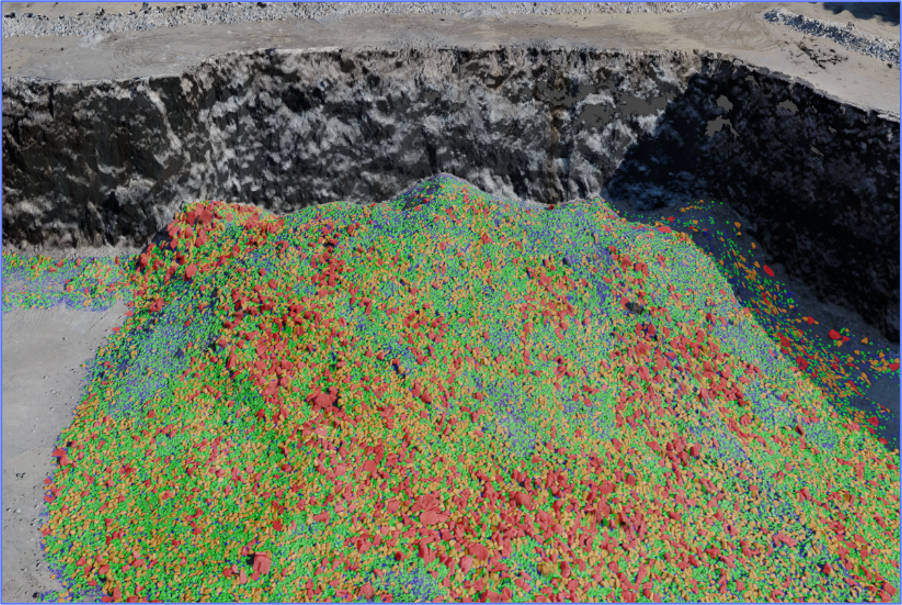
Blast Movement Analysis
Muck pile Analysis measures the material movement and correlates it to the designed and as drilled holes. See cross sections of the pre-blast bench and blast plan, as drilled hole information and overlay that data on the post blast bench and the muck pile. The software measures distance, trough drop, and center of mass. Did the rock move the way you wanted it to?

Back Break Analysis
Backbreak analysis overlays drill designs to measure the distance and volume of back break from the existing back row of a shot to the newly formed face.
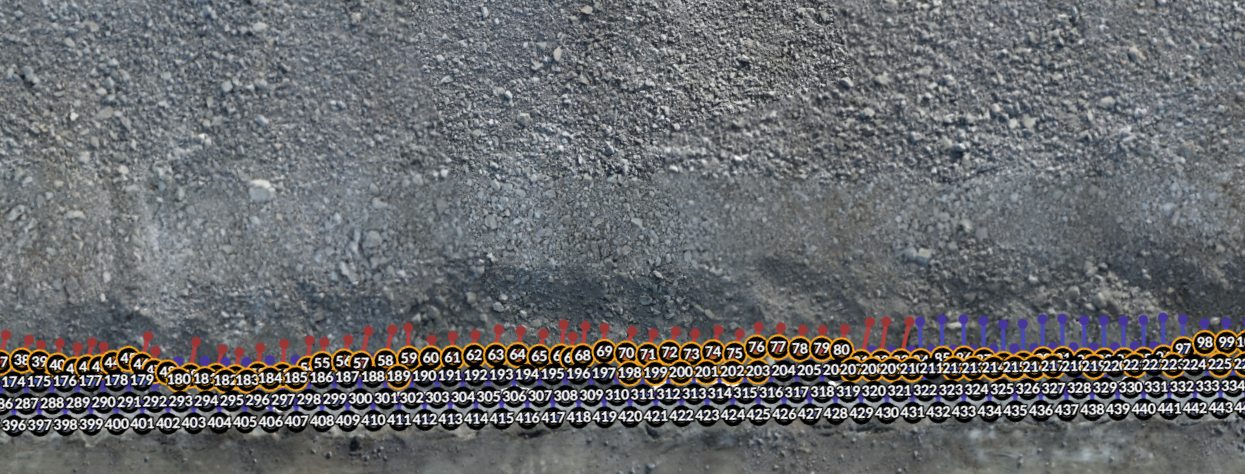
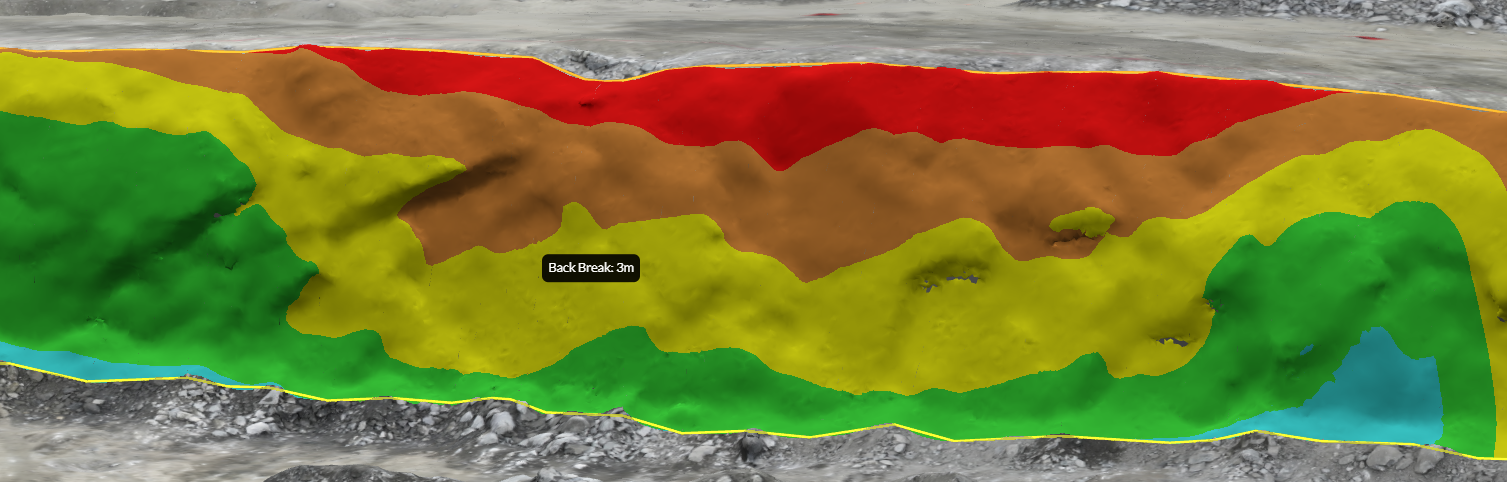
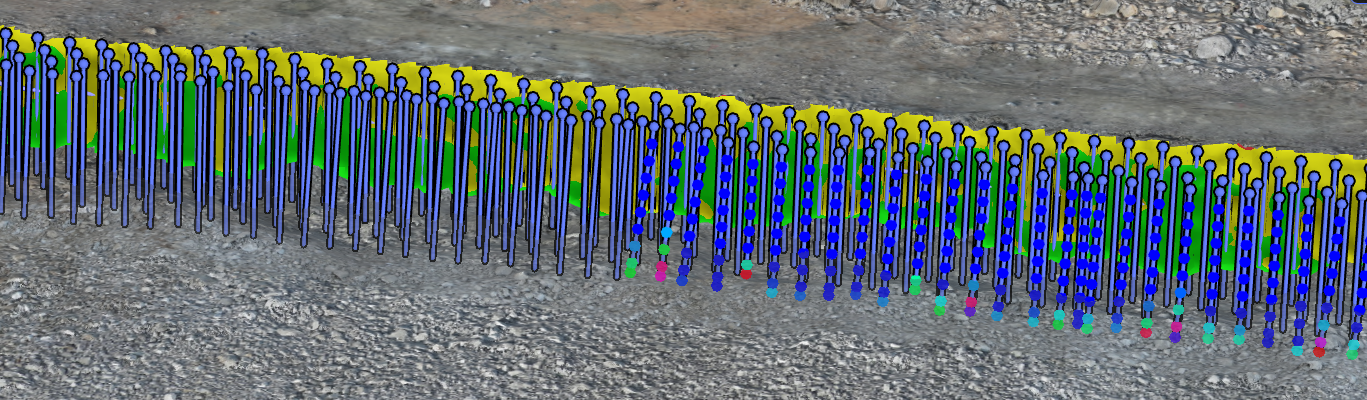

Making the Most of Your D&B in 2025
If your new years resolution is to improve operations (and even if it’s not), a good place to start is with these three powerful tools.
With these three tools, operations can significantly improve their blast performance. The first steps to optimize your operations is to collect the data and measure performance. Being able to host all of the blast data in one platform allows engineers to make correlations and improvements much quicker than previous workflows. Pair the analysis with Artificial Intelligence and you have a recipe for success, powered by Strayos.

New technologies are rapidly changing the drilling, blasting, mining, and aggregates industries, empowering them in ways never before possible. Make sure you are taking advantage of the best tools available.
Check out our 2 Free E-books on AI applications for the drilling, blasting, and mining industries to see all the amazing advances that are available.
AI Guide for Drilling and Blasting
AI Guide for Mining
Watch our videos:
YouTube