The Future of Material Handling: Turning Conveyors into Smart Systems
The Future of Material Handling: Turning Conveyors into Smart Systems
Conveyor systems are the unsung heroes of material transport. They’re the backbone of countless industries, from mining and manufacturing to ports and recycling centers, silently working to keep operations running smoothly. Conveyors are crucial for moving materials efficiently and consistently.
While often overlooked, these systems are more than mere material movers. They're critical transfer points that can significantly impact overall operational efficiency, especially in some underground mines where they serve as the sole conduit for material extraction.
These systems are more than just material movers- they’re opportunities.
In today’s competitive landscape, maximizing the efficiency of conveyor systems can significantly impact productivity and profitability. So how do we revolutionize these vital systems without disrupting production? The answer lies in advanced technologies that are redefining conveyor management.
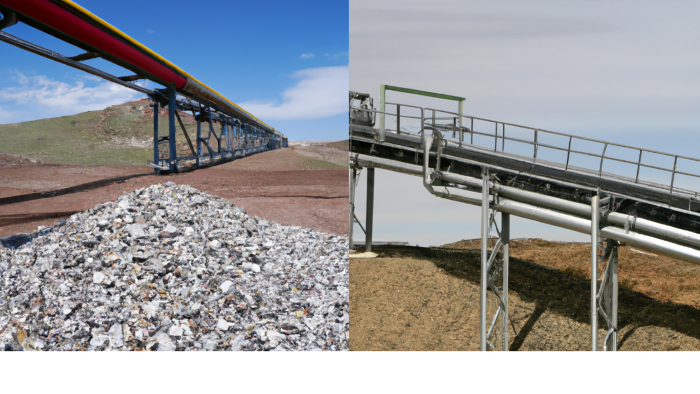
Advanced Measurement Technologies
1. Belt Scales: Precision Weighing on the Move
Belt scales deliver continuous real-time weight measurements of materials on the move. These sophisticated devices can be seamlessly integrated with Programmable Logic Controller (PLC) systems and provide precise data for production tracking, inventory management, and process control.
Key Benefits:
- Continuous weight monitoring
- Easy integration with existing control systems
- Improved inventory management
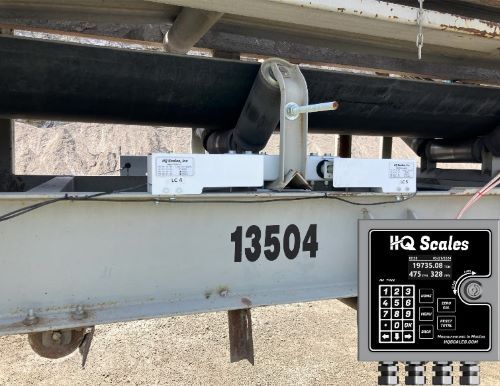
2. Volume Scanners: 3D Insights into Material Flow
Volume scanners, mounted above the conveyor, utilize LiDAR or RADAR technology to offer a no-contact solution for monitoring material flow. By providing detailed volumetric data, these scanners offer real-time insights into material distribution.
Key Benefits:
- Real-time volume measurements
- Non-intrusive highly efficient monitoring
- Enhanced material flow optimization
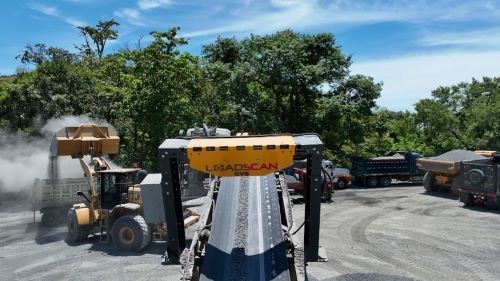
3. Fragmentation and Particle Size Distribution (PSD) Systems: Quality Control in Motion
Fragmentation and Particle Size Distribution (PSD) systems bring quality control to the conveyor belt. These AI-driven tools analyze material size distribution, offering invaluable insights into production quality and consistency. More over they identify foreign objects and oversized material in real time allowing for milling optimization. Many of these systems are now being linked to other critical systems related to production for holistic operational improvements.
Key Benefits:
- Early detection of inconsistencies and foreign objects
- Real-time quality assurance
- Integration with upstream processes
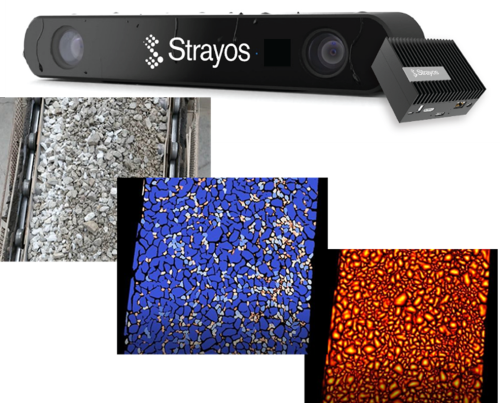
Synergizing Technologies for Maximum Impact
By combining these technologies, mining operations can unlock a new level of efficiency and control:
- Real-Time Density Calculation: Pairing belt scale data with volume scanner measurements allows for instant density calculations, providing crucial information about material properties.
- Proactive Quality Management: Systems like the Strayos Netra utilize AI and Machine Vision to monitor particle size, enabling real-time adjustments to processes like blasting and crushing.
- Comprehensive Performance Monitoring: Integrating these systems creates a powerful centralized dashboard for monitoring production efficiency, from blast performance to product consistency.
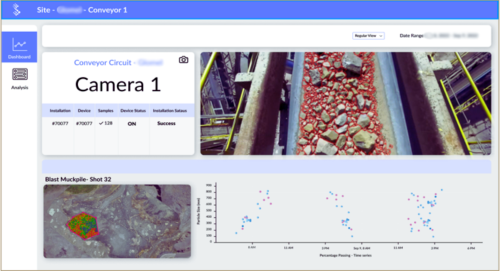
The Strayos Netra System: The Cutting Edge of Conveyor Monitoring
At the forefront of the conveyor monitoring technology is the Strayos Netra System. Designed to turn conveyors into intelligent components of the production chain, this AI-powered system goes beyond simple imaging:
- Intelligent Analysis: The system flags any out-of-spec materials in real time.
- Custom Alerts: Immediately notify operators of issues like foreign objects or oversize.
- Predictive Insights: AI-driven analytics anticipate potential problems, allowing operators to take proactive measures before they impact production and thus minimize downtime.
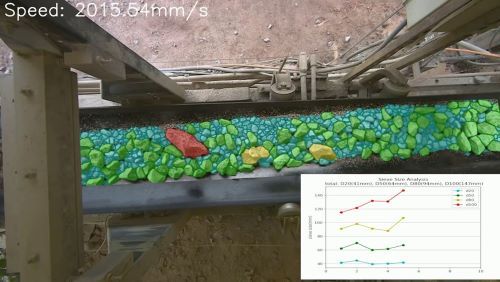
Transforming Conveyors into Smart Systems

By leveraging these advanced technologies, mining operations can transform their conveyor systems from simple material transporters into intelligent, data-driven powerhouses. The ability to monitor weight, volume, and material size in real-time enables:
- Faster, more informed decision-making
- Proactive improvements
- Improved product quality & consistency
- Optimized equipment performance
- Enhanced overall site productivity
In the competitive world of mining, where efficiency isn’t just an advantage—it’s a necessity, turning your conveyor into a smart conveyor system creates a significant edge. With smart conveyor monitoring, you can turn your conveyor into a strategic asset.
Intelligent conveyor systems are the future of material handling, and in this industry, knowledge really is power.
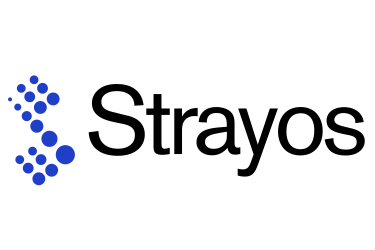
New technologies are rapidly changing the drilling, blasting, mining, and aggregates industries, empowering them in ways never before possible. Make sure you are taking advantage of the best tools available.
Want More?
Check out our 2 Free E-books:
AI Guide for Drilling and Blasting
Don't feel like reading? Watch our videos:
Or Follow Us on Social Media: